
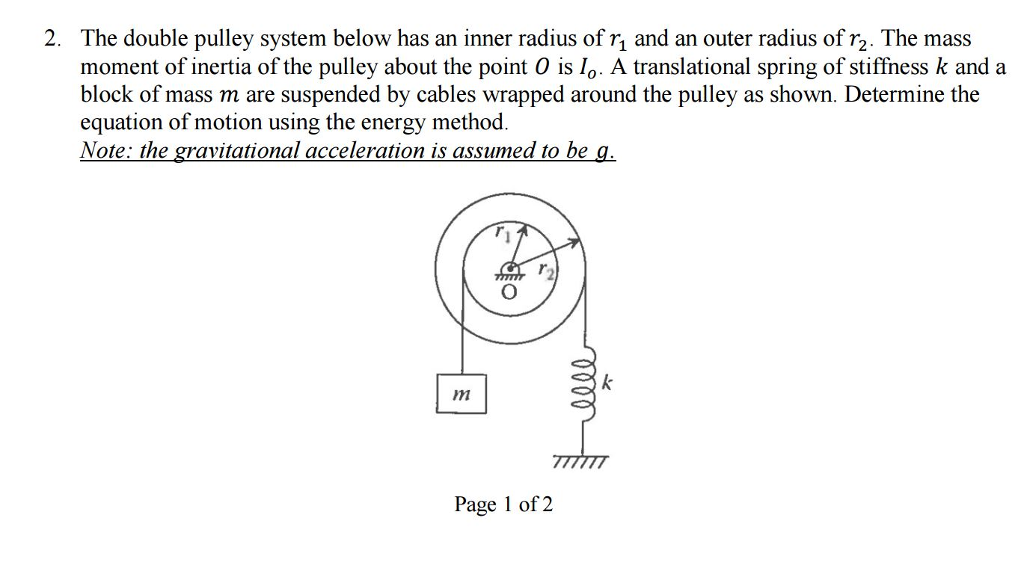
In this case, the total inertia of the moved mass (applied load, belt, pulleys, and coupling) should be divided by the square of the gear reduction, and then the inertia of the gearbox should be added. It’s common for belt driven systems to use a gearbox to increase torque, reduce speed, and reduce the inertia of the load reflected to the motor. J ph = inertia of hollow cylinder (pulleys, coupling) (kgm 2) Keep in mind that although the pulleys may have the same diameters (and radii), if one pulley is toothed (driven) and the other is smooth (idler), as is the case in many belt driven actuators, they will have different masses and, therefore, different inertias.Īlthough the solid cylinder approximation shown above is typically sufficient, more accurate inertia values for the pulleys and coupling can be found by taking into account that these components have a center bore and using the inertia equation for a hollow cylinder: J p = inertia of solid cylinder (pulley, coupling) (kgm 2) The pulleys and the coupling can be treating as solid cylinders that rotate about their own axes, and their inertia can be calculated as: (Be sure to use the full, circular belt length - not just the length of the stroke.)Īlso, remember that the applied load is typically mounted to the belt via a carriage or table, so the mass of this part should be included in the mass of the applied load. The Cornell biped is designed to be highly. R = radius of driven pulley (m) The belt and the load can be considered a point mass that rotates around the driven pulley.īelt manufacturers typically provide mass (or weight) information per unit length, so the mass of the belt can be found by multiplying the mass per unit length by the total length of the belt. If more than one torque acts on a rigid body about a fixed axis, then the sum of the torques equals the moment of inertia times the angular acceleration: i. While no machine built today realizes the union of these attributes, several robots demonstrate one or more of them. J L = inertia of belt and applied load (kgm 2) The applied load and the belt can be modeled as a point mass that rotates around the driven pulley, and their inertia can be calculated as:

Since inertia depends upon the axis around which the component rotates, we can start by considering the applied load and the belt together, since they both rotate around the axis of the driven pulley.

The inertia of each component can typically be estimated with sufficient accuracy by using the standard inertia equations for simple shapes. Find the moment of inertia when this object rotates relative to an axis that is perpendicular to the rod at (a) one end and (b) the center. In belt-driven linear motion systems, the motor has to overcome not only the inertia of the applied load, but also the inertia of the belt, pulleys, and motor coupling. In order for a motor to accelerate or decelerate a load, it must overcome the load’s inertia, or resistance to change in motion, as explained in Newton’s First Law.
